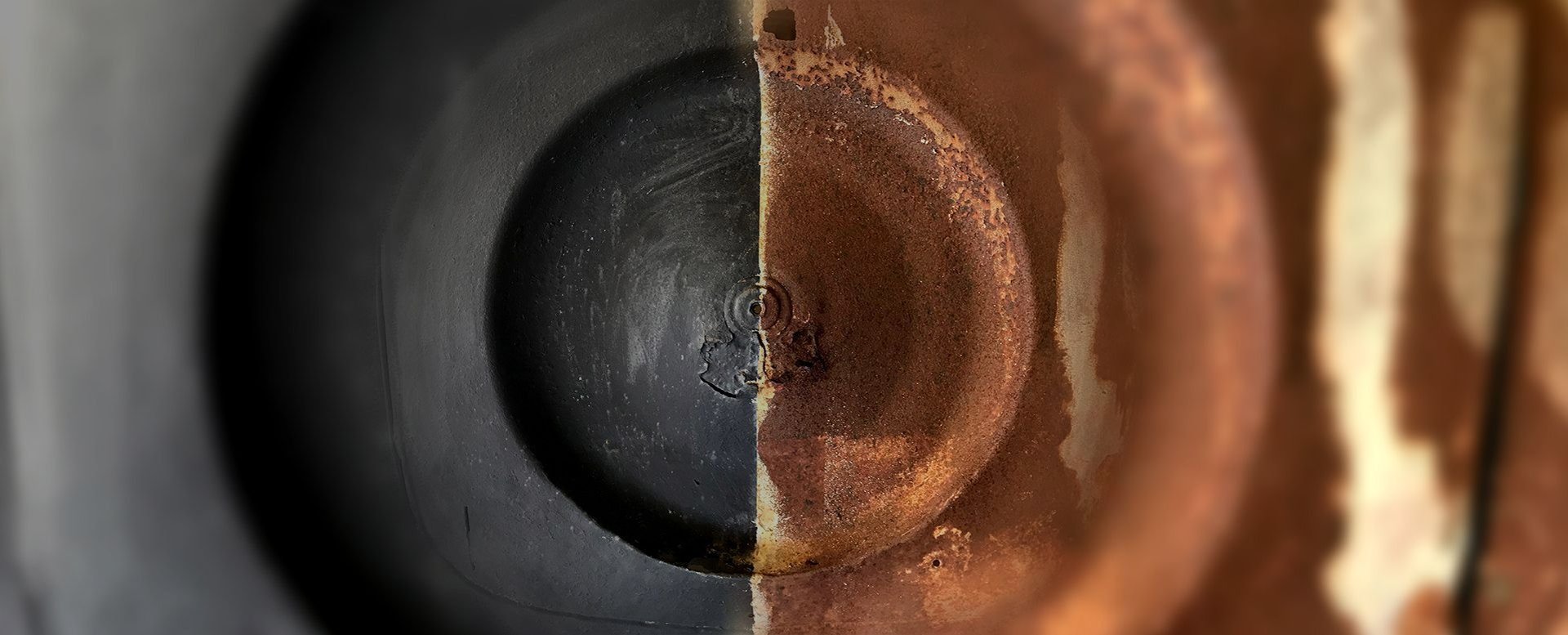
Aircraft / Aviation Corrosion
The Aviation Industry Has Had To Deal With Corrosion-related Airframe Problems For Decades.
The metals making-up a typical aircraft are prone to several different types of corrosion, and long service life compounds these problems – it is estimated that one in four airplanes is over 20 years old.
Up to the 1990s, little attention was payed to aircraft corrosion. Among the first aircraft to incorporate corrosion prevention by design was the Boeing 777, manufactured since 1995.
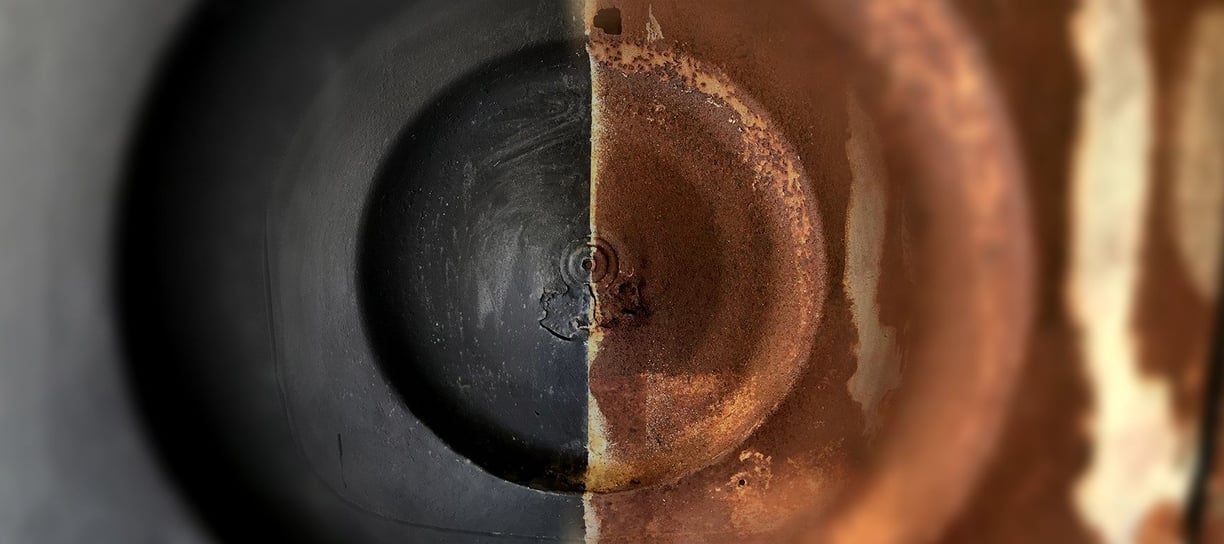
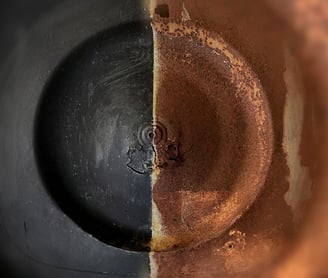
What Factors Accelerate Corrosion
The environment – The environment under which an aircraft operates greatly affects its corrosion characteristics. A marine environment with its sea-water-laden air is the most detrimental, a desert environment the most benign. Temperature also have a significant effect on the rate of corrosion – a hot humid climate being the most detrimental.
Extreme temperature and pressure cycling– By the nature of its service an airplane undergoes large cyclical temperature and pressure changes, as it climbs into the high atmosphere or lands at its destination. Temperatures in the high atmosphere, even in tropical latitudes, may reach -40°C, and pressures can drop as low as 0.2 atmospheres.
This causes:
Ambient moisture to condenseon the aircraft – on its outer skin, in its inner structural surfaces, and on important components, such as electrics and landing gear; moisture then becoming trapped inside these complex structures;
Seals to leakover time, resulting in the penetration of moisture (driven by pressure differentials) even into the nominally sealed areas of the structure; this happens gradually, over a long timescale.
Foreign matter– such as battery acid spillage, caustic cleaning solutions, engine exhaust residues (due to its sulphur content), atmospheric dust and soil.
Leaking lavatories and galleys– sometimes not easily detected, cause the accumulation of humidity in inner structures.
And as the aircraft ages, the cumulation of these factors make the problem of corrosion more severe.
What Are The Mechanisms Of Corrosion?
Filiform surface corrosionis observed as under-paint random thread-like filaments, with the paint often bulging and blistering. This is caused by cracks in the paint which allow the ingress of moisture under the paint.
Galvanic corrosion is caused by two dissimilar metals in the presence of an electrolyte. Aluminium, alloy, extensively used in aircraft, is composed of aluminium plus copper, magnesium and manganese. Exposure of the alloy to water in in the absence of suitable corrosion protection, produces powder-like white or grey corrosion deposits. Carbon fibres in contact with aluminium can also set up a galvanic cell, and thus produce corrosion.
Pitting is the creation of small pits (or holes) on the surface. These pits, however go deep into the thickness of the material, to the extent that structural integrity may be compromised. The corrosion mechanism is that of galvanic corrosion (described above), where the electrolyte becomes trapped in a pit, initially caused by point-damage of the paint layer; as corrosion takes hold, this pit then deepens and traps the electrolyte even more efficiently.
Fretting corrosion is caused by the cyclical relative surface motion between loaded metal surfaces, typically induced by vibration or structural flexing. This often happens around bolts and rivets. The fretting action wears-down the protective or sacrificial layers of the metal and exposes the metal itself to corrosive agents. Cracks are observable on the surface.
Exfoliation – Machined or damaged edges of structural members may have exposed grain ends, that allow corrosion to penetrate the material along planes parallel to the grain surfaces. Corrosion products (which are more voluminous than the original metal), push the grain layers apart, allowing more corrosion to take place. The material is seen to “peel†into leaves, hence the name of this phenomenon.
Stress corrosiontypically occurs in high-strength alloys which intrinsically have a negligible corrosion product. It occurs under conditions of high tensile stress (static or cyclical) in a corrosive environment. Incorrect fits or tolerances due to faulty assembly procedures may cause this.
Micro-biological corrosionis principally experienced in integral aluminium fuel tanks and their piping, in the presence of entrapped water. This water may come from condensation of humid air inside the fuel tank or may have been inadvertently introduced in the kerosene as an impurity. Fungi grow at the water / fuel boundary, especially during periods when the aircraft is in storage. Acidic digestion products of the organisms attack the corrosion-protection layer of the inside surfaces of the tank and of the fuel piping.
And What Are The Consequences?
Primarily safety– A corrosion-weakened airframe is more prone to metal fatigue and to catastrophic failure. Corrosion in other components, such as landing gear, engine parts and electrics can also compromise safety.
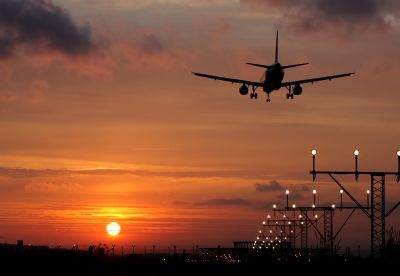
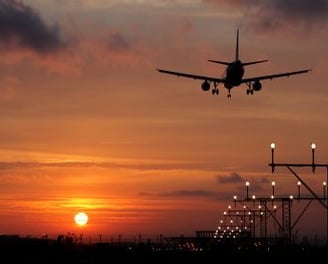
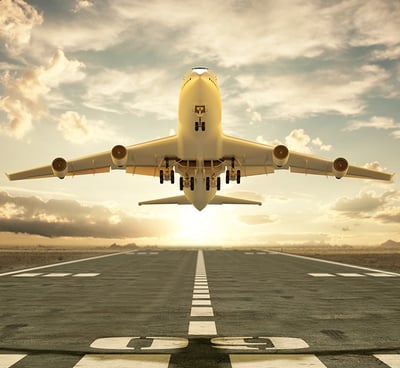
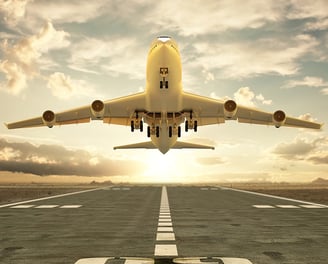
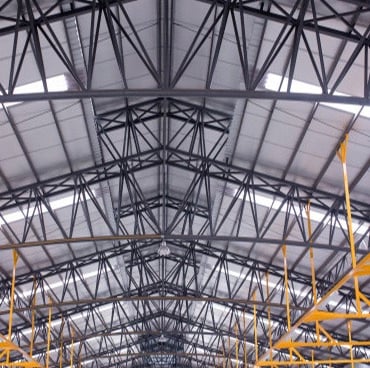
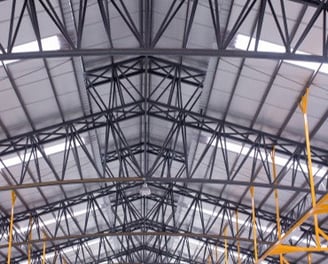
How Much Is Corrosion Costing?
It is estimated that corrosion costs the US aircraft industry $2.2 billion, which includes design and manufacturing ($0.2 billion), corrosion-related maintenance ($1.7 billion), downtime ($0.3 billion). (Corrosion Costs and Preventive Strategies in the United States, Publication No. FHWA-RD-01-156, US DEPT OF TRANSPORTATION, FEDERAL HIGHWAY ADMINISTRATION).
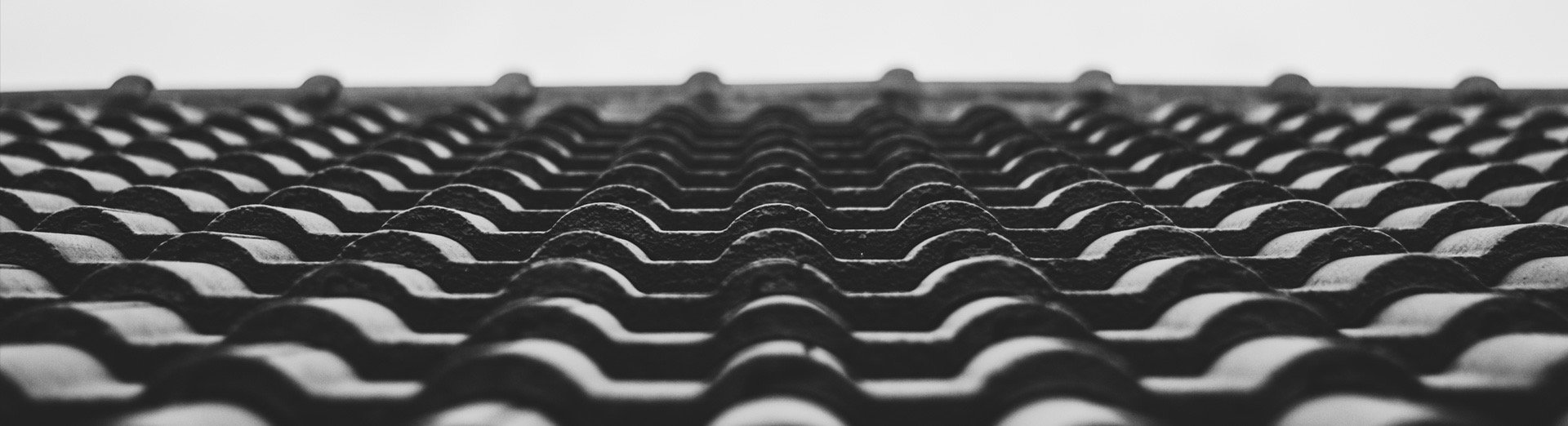
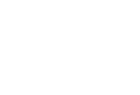
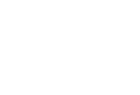
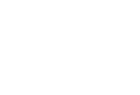
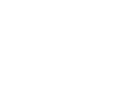
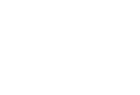
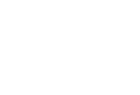
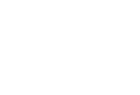
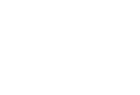
+1234567890
© 2025. All rights reserved.