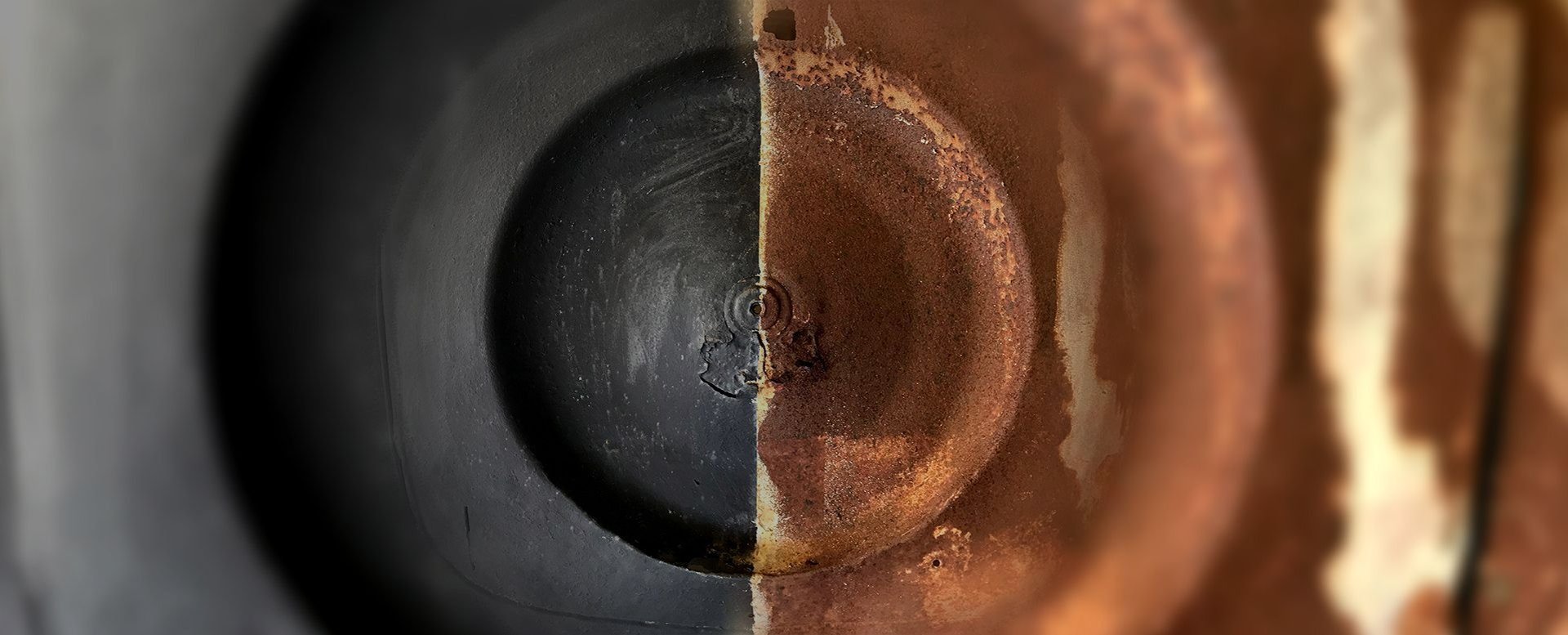
Corrosion In The Chemical Industry
During Production Of Aggressive Chemical Like Acids, The Metallic Equipment For Transportation And Storage Is More Likely To Be Damaged By Corrosion Process.
What Common Materials Used In The Chemical Industry Drive Corrosion?
Chemical industry corrosion is mainly caused by the liquids and gases used in chemical processes. They corrode the processing apparatus and the storage containers from the inside by attacking their inner metallic surfaces. Two types of substances dominate the chemical industry: Concentrated sulphuric acids and organic acids, each bringing particular corrosion problems.
Concentrated sulphuric acid is a key substance in the chemical industry. It is used for making fertilisers and cleaning agents, and as an electrolyte in lead-acid batteries. It is also used in oil refining and mineral processing. It is aggressively corrosive and attacks the inner surfaces of steel tubing and storage containers.
Carbon steel is commonly used in processes involving this acid, because of its economic price and despite its high vulnerability to corrosion. Other steels, such as austentic steel are more resistant to corrosion, but are significantly more expensive. Therefore, even when corrosion-protection measures are implemented, the processing apparatus corrodes away over time.
Organic acids, of which there is an almost unlimited variety of compounds, constitute another important group of substances in the chemical industry. These acids are in general only mildly acidic in comparison to inorganic acids like sulphuric acid (discussed above). However, they cause CO2 corrosion in steel (corrosion caused by the dissolution of iron in carbonic acid solutions containing chloride).
When steel is exposed to a carbonic acid solution, it initially corrodes rapidly. As carbonate scale forms, the corrosion rate decreases, eventually reaching a steady state. If carbonate scale does not form, the corrosion rate will remain high – this depends on the aqueous-phase salinity and temperature. Typically, when the aqueous / brine phase is similar to seawater, this maximum occurs at temperatures between 15°C and 65°C.
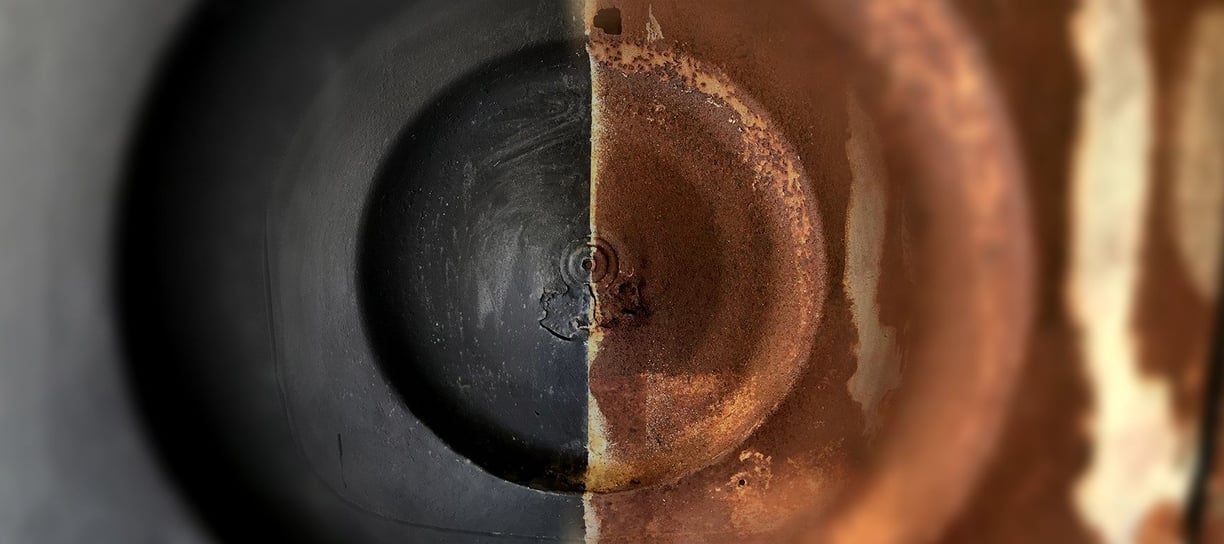
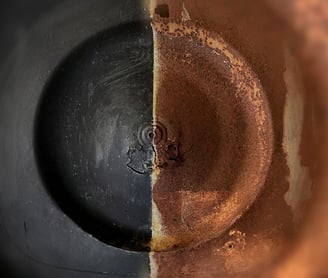
How Does Corrosion Affect Particular Industries?
Food Industry
Food corrosivity can be divided into three categories:
Non-corrosive – for example, milk, fish, meat, oil, fat and cereals Mildly corrosive – foods having a pH of 6 to 7, and having less than 1% salt, for example, wine, beer, carbonated sweet drinks, fruit syrups, soups and canned meat Highly corrosive – foods having a pH of 3 to 5, for example, citric fruit juices, acidic canned fruit, jam, brine-pickled vegetable and fish (with 1–3 % salt), gravies and salad dressings. Corrosion is also caused by the use of cleaning and disinfecting agents, required to maintain food safety standards: Three types of cleaning and disinfection agents are used:
Alkaline – g. caustic soda, alkali phosphates, sodium carbonate and bicarbonate Acidic – e.g. phosphoric, citric and sulphamic acids Oxidizers – e.g. chlorine, nitric acid, ozone, hypochlorite, hydrogen peroxide. Acidic and oxidising substances which flow in the processing plant pipework, and in processing and storage vats cause internal corrosion.
Therefore, the processing and storage vessels for certain types of food are vulnerable to internal corrosion. Products used to clean the processing plants – hygiene is of prime importance in the food industry – may also corrode the plant from the inside.
Pharmaceutical Industry
In the pharmaceutical industry, glass and stainless steel are the principal materials used for the construction of processing equipment. The development of increasingly sophisticated biochemical and pharmaceutical products and processes is being limited by what can be synthesised in stainless-steel containers (where glass is unsuitable).
Despite stainless steel being stronger and more corrosion-resistant than mild steel, stainless steel corrodes over time as its minor ingredients are lost, giving rise to electrochemical potentials which cause the metal to oxidise – thus compromising the quality of the products being manufactured.
Glass is brittle and does not endure thermal cycling well. In many process plants, the glass cracking exposes the underlying iron or steel substrate to the process fluids.
Oil Refining Industry
The inner surfaces of the refining apparatus are attacked by the acidic content of the oil being refined, principally the oil’s sulphur content (sour corrosion), thiol content (mercaptans) and its naphthenic acids. Corrosion is aggravated by the high pressures, temperatures and flows used in the process.
Corrosion predominantly occurs in the crude distillation unit (CDU) and in the high vacuum unit (HVU) where the crude oil is distilled in two steps, at atmospheric pressure and under vacuum, into its major fractions.
How Much Does Corrosion Cost The Industry?
According to the NACE publication “Corrosion Costs and Preventive Strategies in the United States – publication no. FHWA-RD-01-156â€, released by the U.S. Federal Highway Administration (FHWA) in 2002, the direct annual cost of corrosion for the US chemical, petrochemical and pharmaceutical industries stands at $1.7 billion, which is approx. 10% of the total annual direct cost of corrosion in the United States.
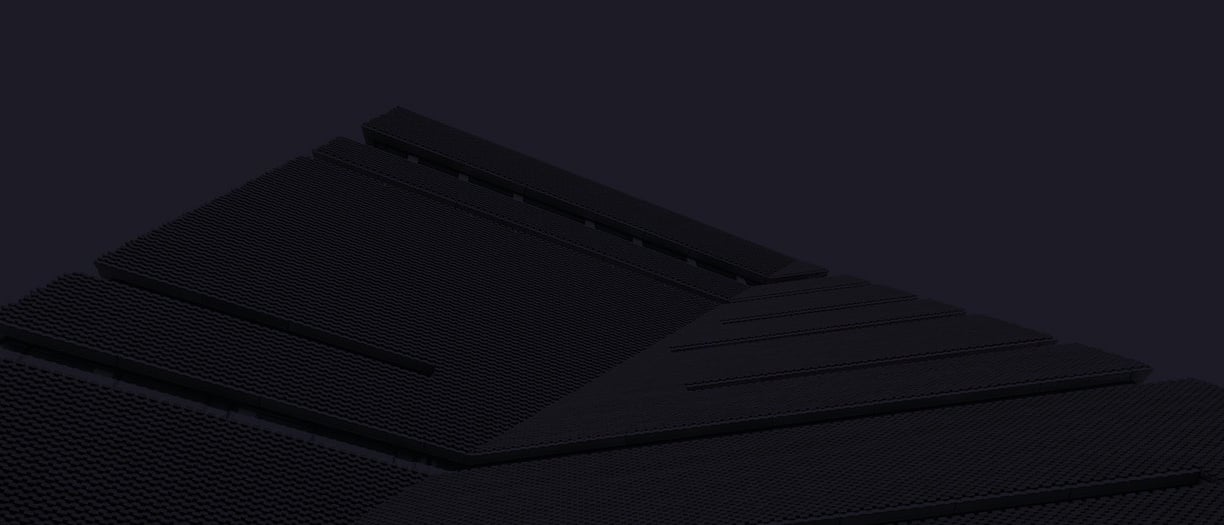
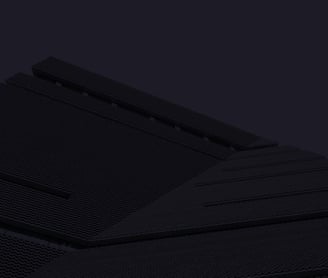
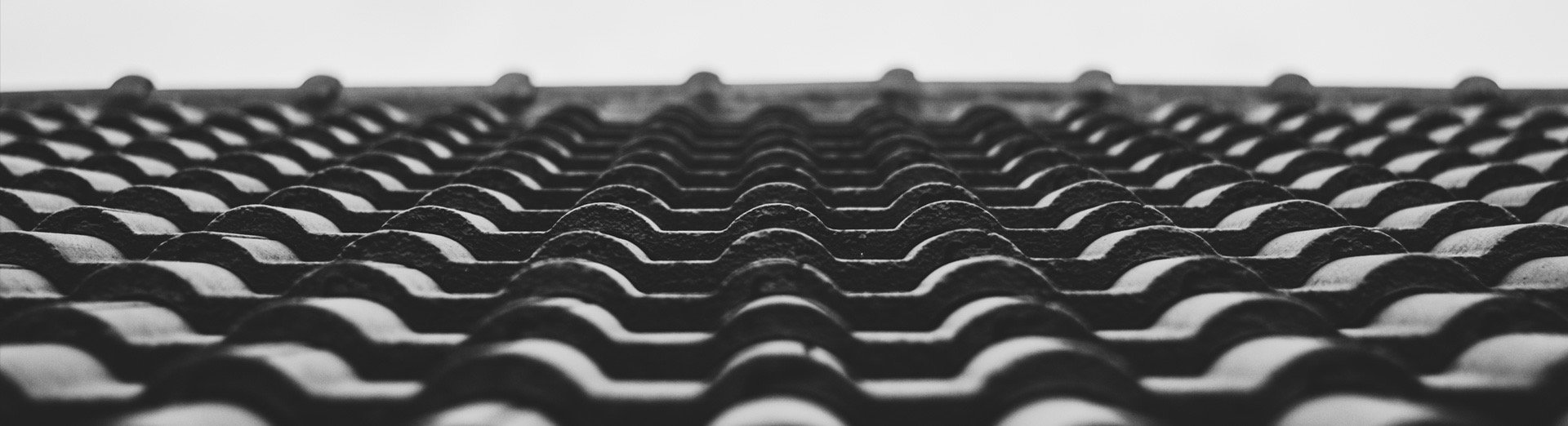
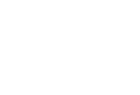
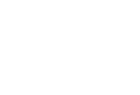
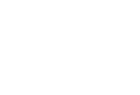
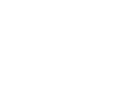
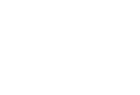
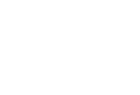
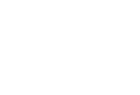
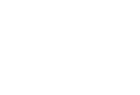
+1234567890
© 2025. All rights reserved.