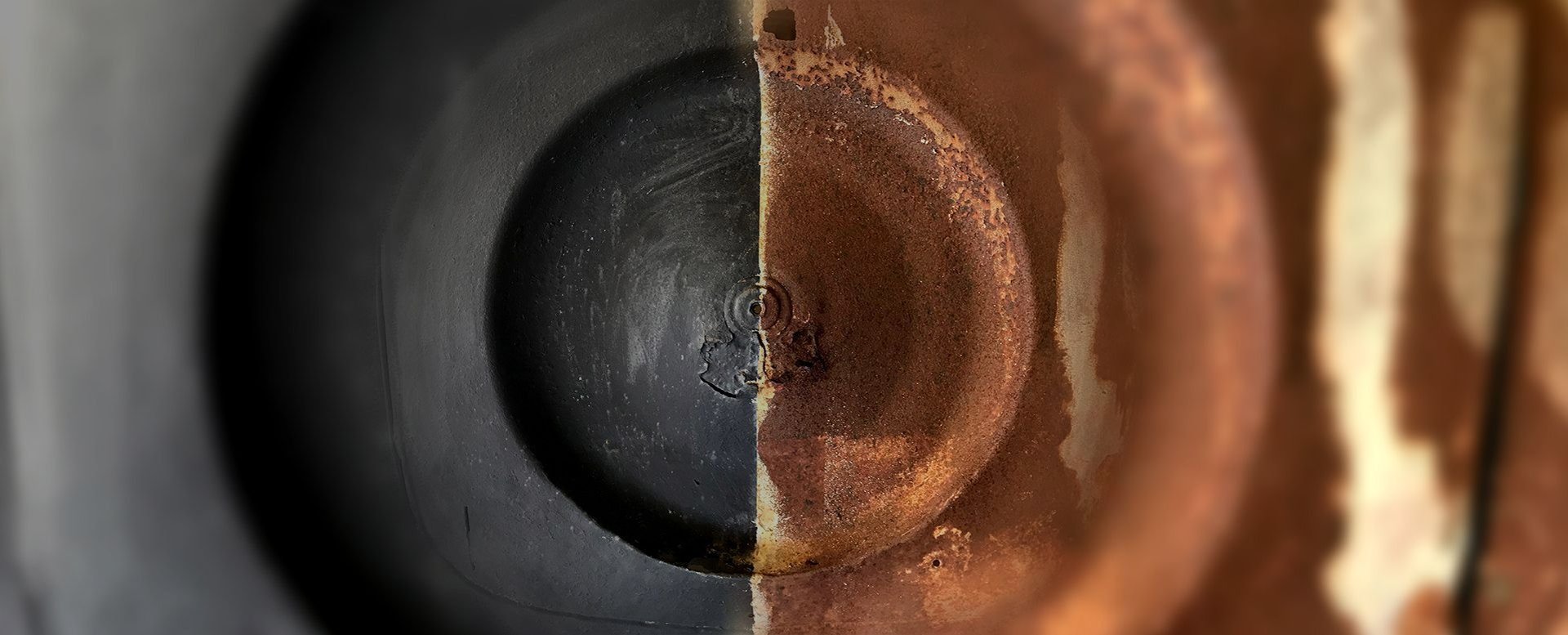
Corrosion In The Gas And Oil Industry
The Popular Saying “rust Never Sleeps†Is So True In The Oil And Gas Industry. Corrosion Starts From The Day Of Manufacture, And Steel Surfaces Whether Easily Accessible Or Not Must Be Protected, Inspected And Maintained.
Oil and gas infrastructure and equipment is mainly made of steel. Extraction is increasingly from the seabed, exposing platforms to a harsh maritime environment. Processing, distribution and storage infrastructure, also principally made of steel, typically operate under harsh environments, and their internal surfaces are exposed to corrosive by-products of oil and gas. All this makes corrosion a major issue in the industry.
The popular saying “rust never sleeps†is so true in the oil and gas industry. Corrosion starts from the day of manufacture, and steel surfaces whether easily accessible or not must be protected, inspected and maintained.
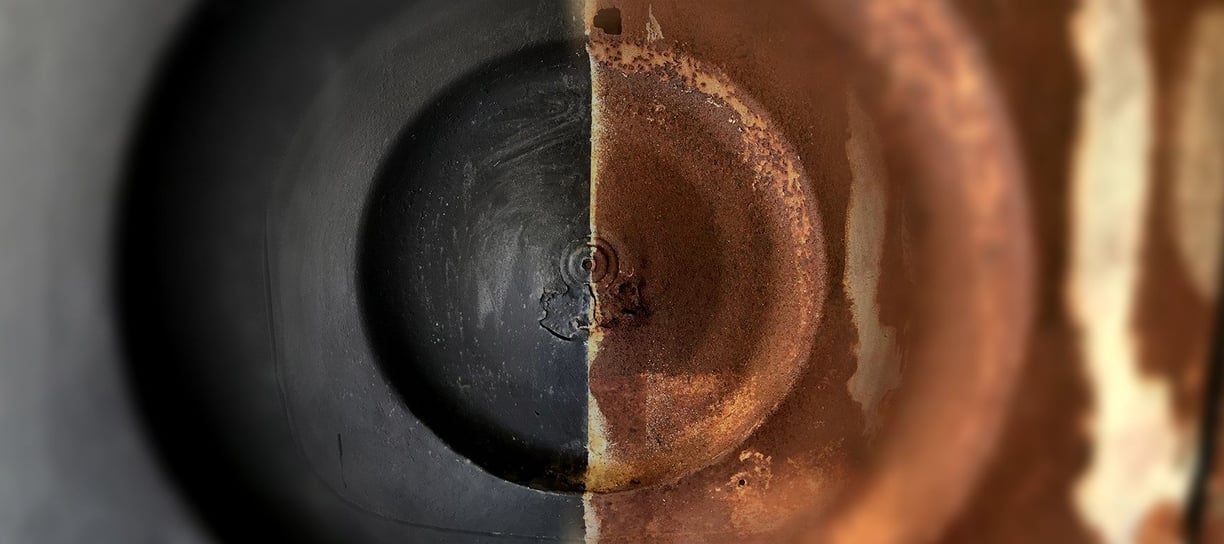
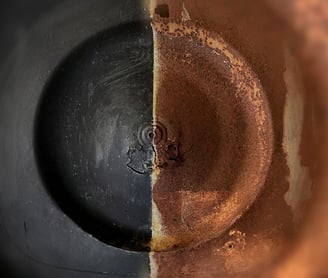
The Changing World Of Oil And Gas Extraction
Before the late 1960s, most oil and gas wells were located on land (mainly in deserts) or in shallow estuaries, bays and swamps.
From the 1970s, North Sea oil and gas came into production at seabed depths of 50 to 100 m, and in an often very stormy marine environment.
From the 1990s, deep-offshore (300 m deep or more), and subsequently ultra-deep-offshore (3000 m deep or more) oil/gas exploitation came on-line. Shell’s Perdido platform in the Gulf of Mexico is such an ultra-deep well.
Today, almost all of the “newer†exploitable oil/gas is deep under the sea, and often thousands of metres under the seabed. The great undersea depths, together with the great depths under the seabed, combined with the salty sea atmosphere, provide a formidable challenge to corrosion protection – i.e., access, inspection and renovation of the protective coating.
Oil Refineries – Complex Plant Attacked By Acid Corrosion From Inside
The inner surfaces of the complex refining apparatus are attacked by the acidic content of the oil being refined. Corrosion is aggravated by the high pressures, temperatures and flows used in the process.
Corrosion predominantly occurs in the crude distillation unit (CDU) and in the high vacuum unit (HVU) where the crude oil is distilled in two steps, at atmospheric pressure and under vacuum, into its major fractions.
The inner surfaces of the steel apparatus react with the oil’s sulphur content, mainly H2S (“sour†corrosion – which also affects pipelines, as explained further on). These inner surfaces also react with the oil’s thiol content (mercaptans) and its naphthenic acids (of generic formula CnH2n-z O2), which are highly corrosive.
High temperature accelerates the corrosive chemical reactions, and high pressure and flow intensify the shear stresses on internal pipe surfaces; this degrades the FeS protective layer, thus facilitating corrosion of the bulk metal.
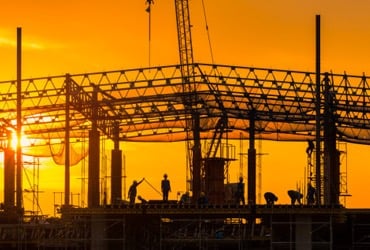
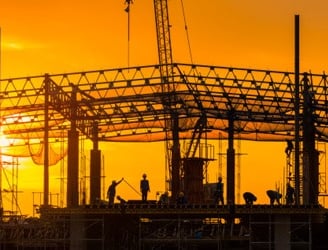
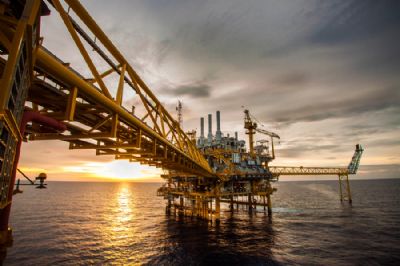
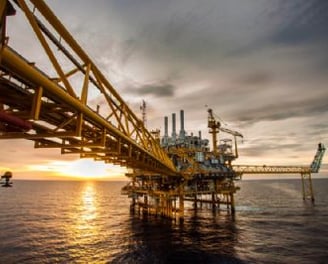
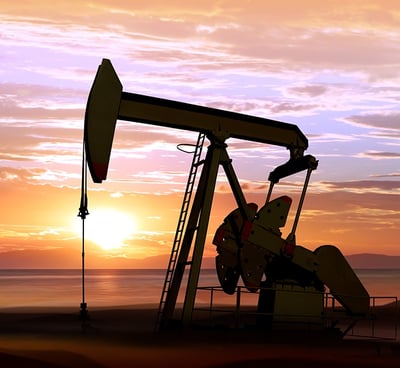
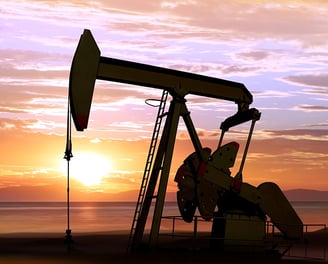
Oil & Gas Pipelines – Attacked From Outside, Eaten-up From Inside
Oil and gas pipelines, whether from the well to the processing facilities, or in distribution network to end-point users, are deployed over- or under- ground, as well as underwater, over vast distances and in varied terrain.
Corrosion caused by the transported substance, whether oil or gas, can be divided into “sweet†and “sour†corrosion: Sweet corrosion takes place in systems containing only carbon dioxide, with a low level of hydrogen sulphide (H2S partial pressure < 0.05 psi). Sour corrosion takes place where the hydrogen sulphide’s partial pressure is above 0.05 psi. H2S itself is not corrosive, but a water-containing gas environment causes reactions which lead to corrosion of the inner surface of the steel pipeline.
Sweet corrosion results in internal pitting of the pipeline, whereas sour corrosion is much more severe, and can compromise the structural soundness of the pipeline, leading to fatigue failure.
Additionally, because of the long runs in unprotected environments, pipelines are exposed to external corrosion attack. All of the above leads to pipeline leakage, with a potential for ecological damage or danger to life.
Storage Tanks And Gas Cylinders – Use And Abuse
Oil and gas storage devices are vulnerable to “sweet†and “sour†corrosion similarly to pipelines, as explained above. In addition, moisture penetration inside the device, and its accumulation in the container bottom aggravates corrosion, especially in the lower part of the container. This moisture may also evaporate in warm weather, and with a fall of external temperature, re-condensate all over the internal surface of the container.
Moisture penetration occurs mainly in the absence of an effective non-return filler valve and/or – for gas cylinders – when they are left open in a totally depressurised state. Domestic gas cylinders are also prone to external corrosion, caused by knocks during transport and when they are placed on damp surfaces while in service.
The Hidden Cost Of Corrosion
Corrosion damage is gradual, and it may take years until significant deterioration occurs; eventually resulting in leaks, equipment breakdowns, and structural failure. All of this has a sometimes-critical impact on: productivity (performance degradation and equipment failure), the environment (pollution through spillage), and above all safety (structural failure, fire, explosion and worse).
Often the day-to-day economics of running an oil/gas installation discourages taking the long-term view with regard to corrosion maintenance – oil price instability causing profit margin fluctuations. In particular, with regard to extraction platforms, as reserves diminish at a particular well and future closure is anticipated, investment in expensive maintenance is discouraged – exactly at the stage when corrosion-protection maintenance becomes critical.
The cost of corrosion protection is a significant item in the maintenance bill of contemporary oil and gas installations and equipment:
Sea-borne extraction platforms, their risers (parts of which may be hundreds or even thousands, of metres underwater), the well and its drilling equipment (inaccessible under the seabed or deep underground) – both the severity of the working environment and the inaccessibility of equipment make inspection and corrosion maintenance very costly.
Refinery plant is very vulnerable to internal corrosion. Due to the complexity of the equipment and the inability to directly reach internal piping, corrosion monitoring and mitigation methods require a substantial outlay.
Pipelines and storage tanks, which are deployed over a wide geographic area and – in the case of domestic gas containers – may suffer abuse by the end-user, require distribution companies to spend time and resources in inspection and repair.
According to a study by the U.S. Federal Highway Administration (FHWA) in 2002 (Corrosion Costs and Preventive Strategies in the United States, PUBLICATION NO. FHWA-RD-01-156 – NACE International), in the USA, the cost of corrosion for gas distribution was estimated to be $5 billion, and for oil & gas exploration & production about $1.4 billion, with $0.6 billion attributed to surface piping and facility costs, $0.5 billion to downhole tubing, and $0.3 billion to capital expenditures related to corrosion.
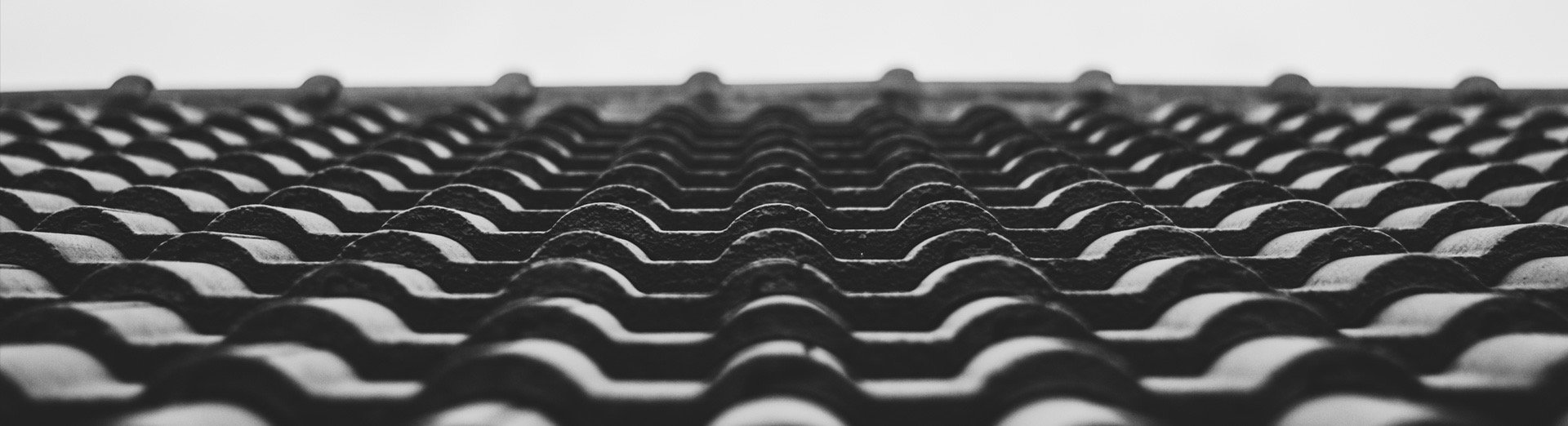
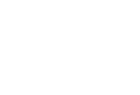
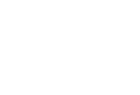
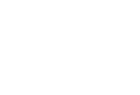
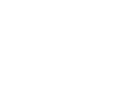
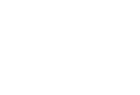
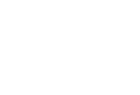
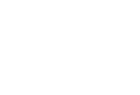
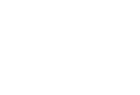
+1234567890
© 2025. All rights reserved.