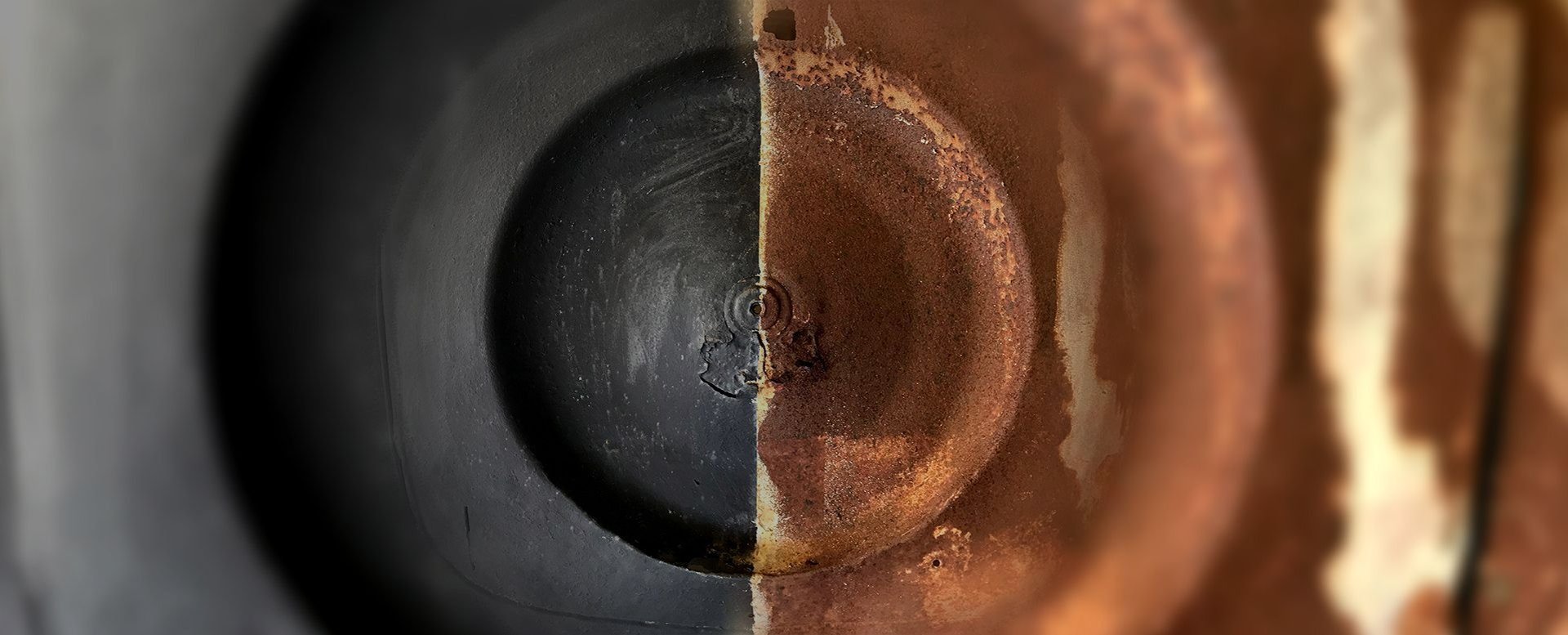
Corrosion In Reinforced Concrete Infrastructure
Today, Steel-reinforced Concrete Is Widely Used In Most Types Of Infrastructure. Buildings, Roadway & Railway Terracing & Support, Bridges, Harbour Installations, Dams.
Since concrete can only take compressive stress, and not tensional stress, it must always be reinforced by internal steel bars, which are seemingly protected from the ravages of the external environment. They are certainly out of sight, buried in the body of the concrete…Out of sight, out of mind? Will they eventually rust? The short answer is yes.
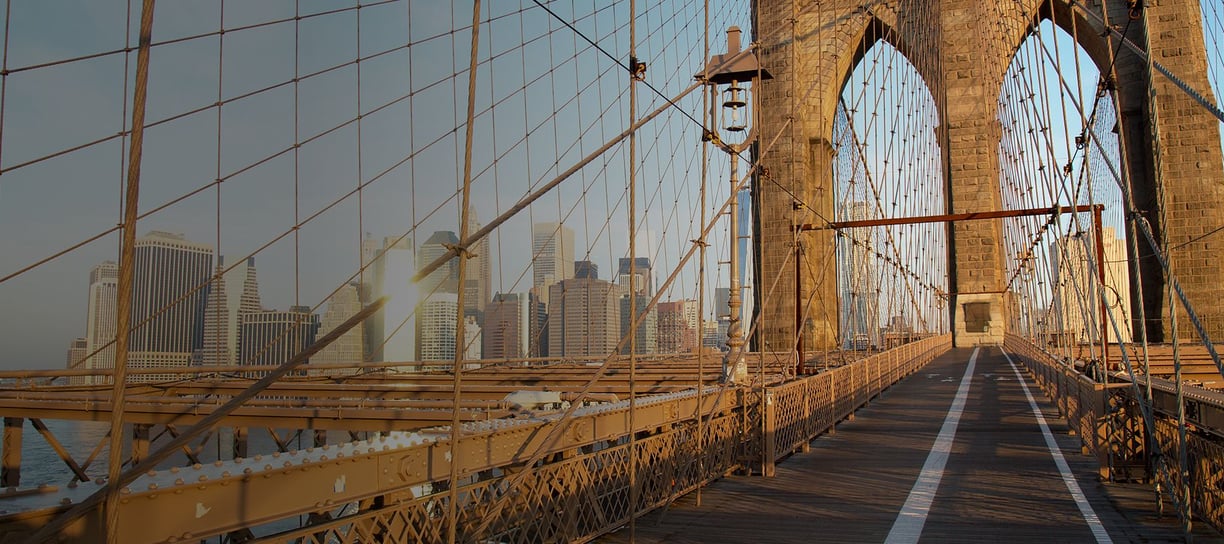
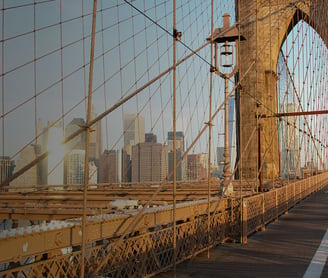
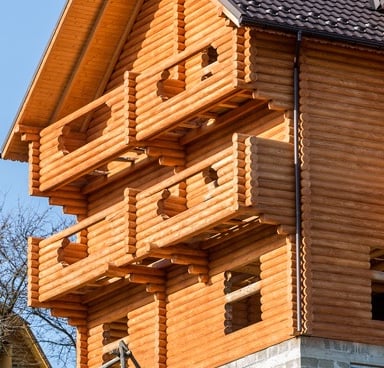
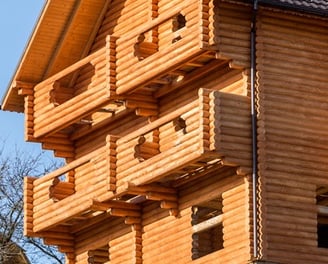
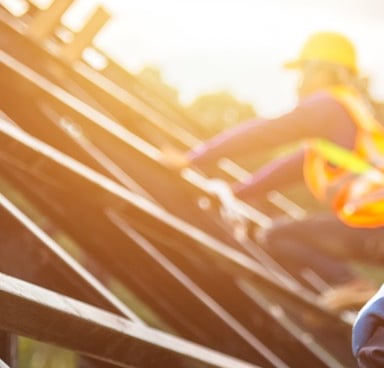
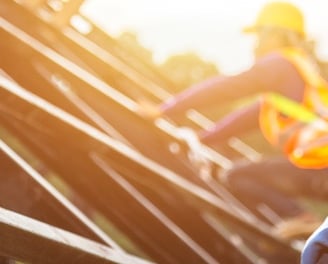
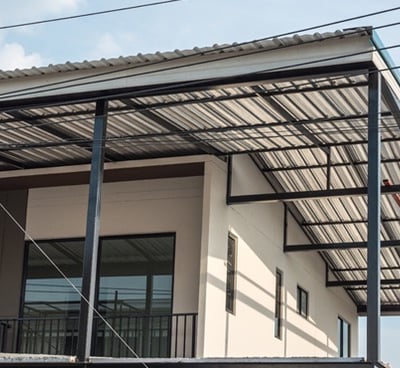
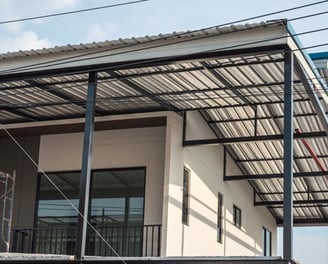
The Mechanisms Of Corrosion
Despite its appearance, concrete is typically wet, and therefore the steel bars are in a wet environment. However concrete is intrinsically very alkaline (high pH), which prevents oxidation of the steel bars buried inside.
A.Contaminants
Anything which neutralises the alkalinity of the concrete, allows oxygen to penetrate the concrete’s complex cement matrix, and eventually reach the steel bars. Common contaminants are:
Chloride ions, found in abundance in sea-salt spray and de-icing compounds (typically salt) applied to roadways in snowy weather
Water-borne atmospheric carbon dioxide reacting with the lime from the cement to form carbonic acid
Sulphur and nitrous oxide, found in urban polluted atmospheres are essentially acidic.
All of the above lead to a loss of alkalinity and thus facilitates the penetration of oxygen through the cement matrix, right down to the steel bars.
B.Mechanical Stresses
Structures are always subject to mechanical stresses: vibration, load changes, environmentally induced stresses (discussed further on). Mechanical stresses cause slight deformation of the concrete, which may lead to micro-cracking. When the concrete cracks, oxidisers can reach the internal steel bars more easily.
C.The Effect Of The Environment
Temperature – In general higher temperatures accelerate any ongoing corrosion process; at sub-zero temperatures the corrosion process is considerably slowed-down.
Humidity – High relative humidity accelerates the corrosion process. The effect of humidity is determined by the Time Of Wetness (TOW), i.e. a measure of the time for which atmospheric conditions favour the formation of a moisture layer on the structure’s surface. Humidity neutralises alkalinity and thereby facilitates oxygen penetration.
Marine environment– High humidity conditions, together with sea spray salinity, throws an abundance of chloride ions at the concrete, which neutralises alkalinity and thereby facilitates oxygen penetration.
Soil exposure– When water freezes, its volume expands by a little less than 10 percent. Any humidity present in small cracks will therefore force these cracks open upon freezing. Repeated freeze-thaw cycles, caused by cyclical ambient temperature changes will widen the cracks, thus facilitating oxygen penetration to the buried steel bars.
Environmental differences– Differences in oxygen concentration, acidity, moisture or salinity between different parts of the structure facilitate the penetration of oxygen into the cement matrix.
D.Stagnant Water And Drainage
In many concrete structures, water (typically rain water) runoff is deficient, either because of the physical shape of the concrete elements, or because drainage channels have become obstructed. In either case, stagnant water pools collect in certain locations – salt water in marine environments – and the concrete’s alkalinity at these locations is diminished, leading to oxygen penetration to the buried steel bars.
E.Feedback Loop
When an internal steel bar starts to corrode due to any combination of the above, its volume increases. This generates pressure inside the concrete element, widens any existing cracks and generates new cracks from the inside to the outside. This in turn increases the exposure of the steel to oxygenation and accelerates the corrosion process. Thus, further corrosion is also accompanied by further cracking. Therefore, over time, the corrosion process is accelerated.
Consequences Of Corrosion
Steel corrosion inside the concrete element has two main consequences:
Corrosion-induced volume changes of the steel bars inside the concrete cause the concrete to crack and eventually break-up.
The steel bars themselves become weaker and more brittle by corrosion, leading to further loss of strength of the concrete.
Both of the above lead to the likelihood of structural failure, especially during severe external conditions, or heavy loading – many recent road-bridge failures have been attributed to this.
How Much Does It Cost?
According to “Corrosion Costs and Preventive Strategies in the United States†(FHWA, Publication No. FHWA-RD-01-156, dated 03/2002), the estimated annual direct cost of corrosion in the United states is as follows (based on a study by CC Technologies Laboratories, Inc. conducted between 1999 and 2001).
Highway bridges: $8.3 billion, consisting of $3.8 billion for the replacement of structurally-deficient bridges over the next 10 years, $2.0 billion (including a cost of capital) for the maintenance of concrete bridge decks, $2.0 billion (including a cost of capital) for the maintenance of concrete substructures (minus decks), and $0.5 billion for maintenance painting of steel bridges. Through life-cycle analysis, it is estimated that indirect costs to the user attributable to traffic delays stand at more than 10 times the direct costs enumerated above.
Waterways and ports: $0.3 billion. Typically, corrosion is found on docks, piers, mooring structures, bulkheads, retaining walls, and navigational aids (such as lighthouses). Corrosion costs for these structures are not formally monitored. However based on figures obtained from the U.S. Army Corps of Engineers and the U.S. Coast Guard, the annual corrosion cost is estimated to be $0.3 billion.

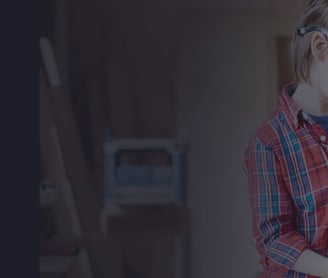
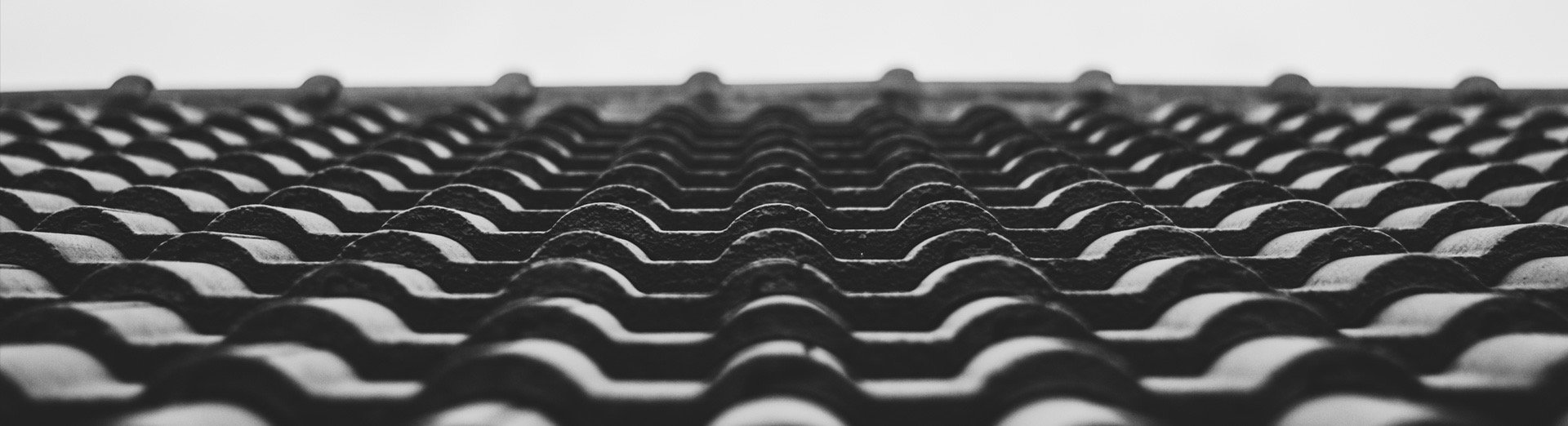
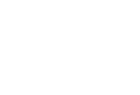
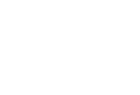
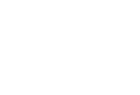
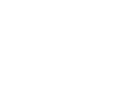
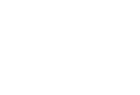
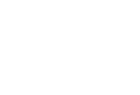
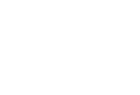
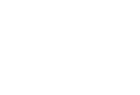
+1234567890
© 2025. All rights reserved.